Discarded automobile tyres are major contributors to the mounting garbage around the world. Because of the hard characteristics of the tyres, they are often very difficult to get rid off. Many people and businesses resort to burning them but this causes even more damage to the environment because of the huge amounts of carbon dioxide that are released into the atmosphere. However, there is a more environment-friendly way of discarding and recycling used tyres. The process is called pyrolysis and it involves heating the tyres in a reactor vessel which will eventually break down the rubber into smaller molecules. The best part about this process is that it produces valuable and reusable by-products like oil, carbon black, and gas. In the following pyrolysis tire recycling system project report, we’re going to look into how the process works and how it will benefit the environment.
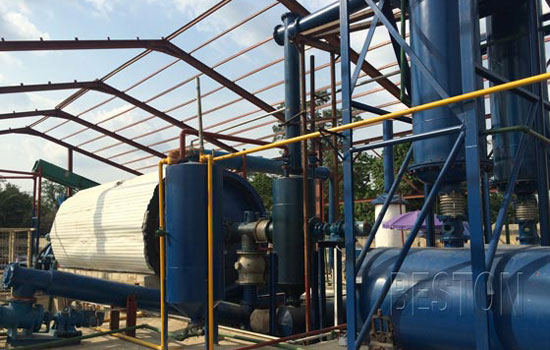
scrap tire pyrolysis plant
The tyre pyrolysis process is quite simple which is why many companies are now using it to recycle their discarded tyres. Basically, you need a plant composed of several machines that will be used to recycle the used tyres. The most important part of the plant is the reactor vessel where the tyres will be heated, softened, and broken into much smaller molecules. The reactor vessel is unique due to the fact that it doesn’t make use of oxygen to break down the rubber. It simply vaporizes the the tyres. This is why every containerised pyrolysis plant project report doesn’t report unnecessary emissions or wastes. In short, the process is safe and completely clean.
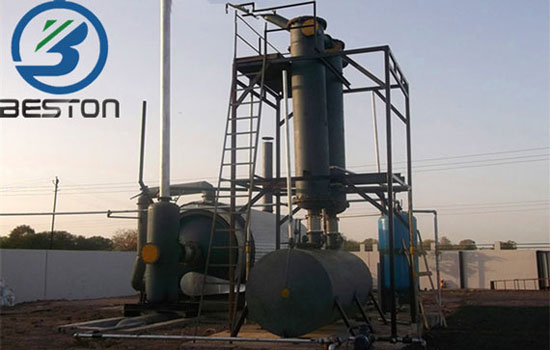
waste tyre recycling pyrolysis plant
The tire recycling plant cost is not that high. With an experienced engineer, a team of knowledgeable fabricators, and someone who knows the pyrolysis process, you can come up with a working prototype that can deal with a huge pile of used tyres. A standard-sized plant can accommodate up to ten tons of discarded rubber tyres. In addition, the plant has an average service life of six to eight years. This lifespan can be lengthened if you carefully maintain the plant’s reactor vessel which is the heart and brain of the plant.
The process produces four valuable products. A tyre recycling pyrolysis plant project report won’t be complete without an enumeration of these important by-products: https://www.bestongroup.com/tyre-to-oil-plant-cost/. The great thing about these end products is that they can be reused as alternative energy sources. Majority of the end products is composed of crude oil which you can either sell or you can turn it into diesel and gasoline. Another product of the process is carbon black which can be used in the production of industrial materials like cable jackets and pipes. The process also produces steel wire and gas. The wire can be used in iron and steel factories while the gas can be recycled to be used in furnaces and other heating machines that make use of gas.